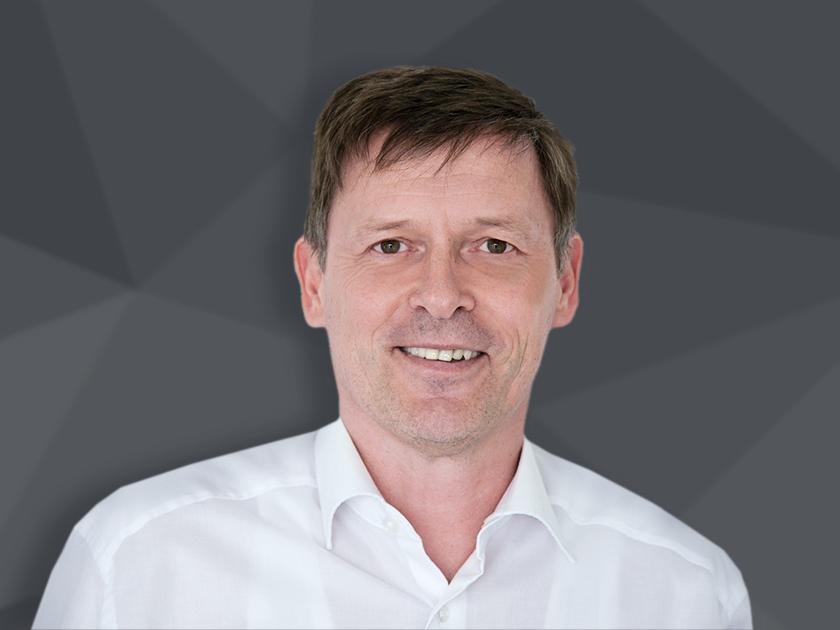
How Finetech supports a high power fiber laser manufacturer to implement high-accuracy assembly processes for in-house developed high power diode pumps and to transfer them from prototyping into automatic series production.
Convergent Photonics develops and distributes High Power Industrial Fiber Laser Solutions for material processing applications. Finetech has supported Convergent Photonics in the development of powerful multi-emitter modules right from the start and has helped them to successfully bring the assembly process into production using automatic die bonder systems.
The cooperation between Convergent Photonics and Finetech started in 2015. Finetech provided the R&D bonder FINEPLACER® lambda for the in-house development of a power laser module. This system was used for the complete implementation of the initial laser assemblies as well as the pilot production of the multi-emitter laser module.
- The edge-emitting laser diodes are placed on a submount (heatsink), with the light-emitting facet aligned to the edge of the submount with micrometer precision.
- A self-aligning placement tool for laser diodes developed by Finetech is used to align the component exactly parallel to the heatsink. The degree of freedom of the tool enables the compensation of form tolerances of the submount.
- For optimal power output and stability, the laser is positioned with a defined overhang in the range of a few micrometers to the edge of the heatsink, the accuracy requirement is ±1 µm.
- The laser diode is bonded via a eutectic gold-tin soldering process. Here an absolutely uniform bond line between laser and heatsink must be ensured.
- For the assembly process of several CoCs (Chip on Carrier) in a module housing, a soldering preform, followed by the actual CoC, is placed and bonded in the module using a “multi-axis compensation tool”. The angular deviation of the CoC from the edge is particularly important. Again, the placement tool allows the form tolerances of the module housing to be compensated. A special soldering process jointly developed by Finetech and Convergent Photonics is triggered in the automatic process sequence by partial energy supply, ensuring an extremely quick realization of the solder reflow.
- Finally, several assembled heatsinks (CoC) are mounted into the module housing with highest precision. Optical bundling of the individual laser beams creates the multi-emitter laser module with a defined total output.
In addition to implementing the application, the challenge was to transfer the production of multi-emitter laser modules to series production. For this purpose, Convergent Photonics opted for the FINEPLACER® femto 2, which allowed them to maintain the level of process reproducibility and accuracy they had achieved during the development stage on the FINEPLACER® lambda, while at the same time being able to integrate the automatic handling and process steps required for series production. Processes already developed could be transferred from the manual development system to the automated bonding platform.
The manufacturing process was made even more efficient with the help of a Finetech production platform. Now all work steps are divided between the machines in the best possible way. While development work continues on the FINEPLACER® lambda, the automatic assembly of laser components onto the submounts is carried out on the FINEPLACER® femto 2. Finally, an automated micro assembly platform by Finetech is used to assemble all CoCs into the laser module housing in an automatic assembly process. The individual CoCs are precisely aligned to the edges, then placed and soldered. In addition, the automated micro assembly platform is also used for other automatic processes: the assembly of carrier sheets, including dispensing adhesive, placing the carrier sheet and curing the adhesive, as well as the subsequent application of sealing adhesive.
As a result, large parts of the development and manufacturing processes are now performed on die bonders supplied by Finetech.
“I joined Convergent Photonics in late 2014 with the mission to manage high power semiconductor laser diode assembly technologies. During these years I’ve had the privilege to develop a strong technical collaboration with Finetech. I’ve been impressed by their technical skills and the top performance of their assembly machines. Finetech is the optimal partner to meet the demanding process and accuracy specifications of high power diode laser assembly.”
Working with Convergent Photonics can be described as very constructive but also quite challenging due to the advanced technological level.
With the help of extensive analyses and evaluations, alternative assembly and bonding technologies for advanced multi-emitters were investigated. In close cooperation, process steps and soldering results were continuously optimized by implementing targeted machine and tool adaptations. This included the use of suitable placement tools as well as powerful low-drift heating plates, which enable particularly short temperature cycles with very high post-bond accuracy. By automating the production stage, handling and process times were once again significantly reduced.
Together, Convergent Photonics and Finetech have successfully transferred a complex assembly application into stable series production and lay the infrastructure for further product developments in the field of power lasers.
Copyright © 2025 Finetech GmbH & Co. KG, All rights reserved.