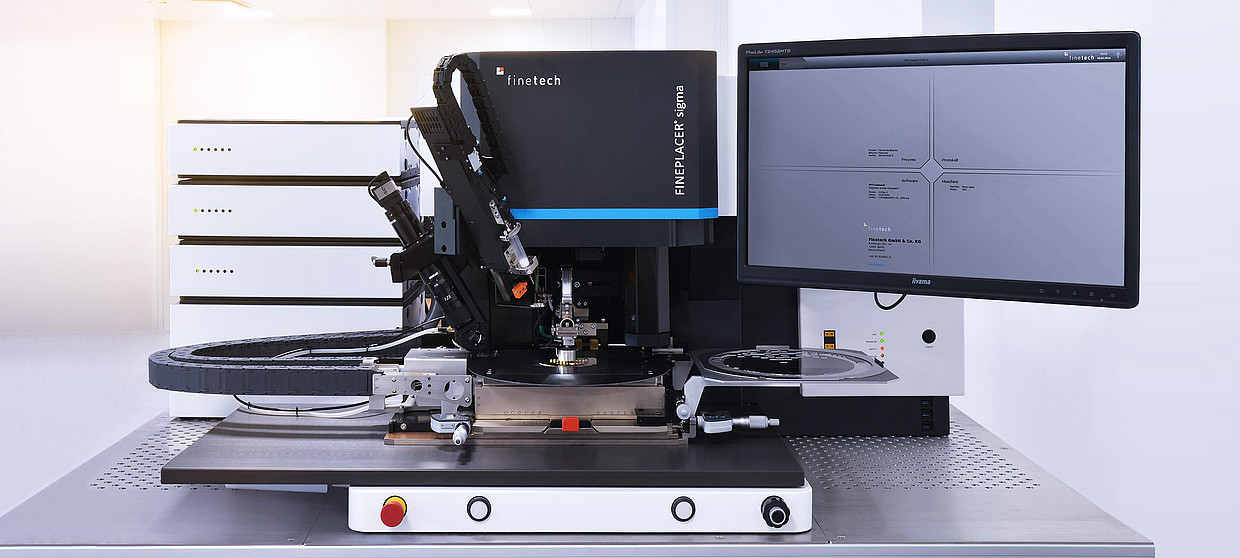
Unrivaled Flexibility for Research & Prototyping
Advanced Sub-Micron Bonder
The FINEPLACER® sigma combines sub-micron placement accuracy with a 450 x 150 mm working area and bonding forces up to 1000 N.
The system is ideal for all types of precision die bonding and flip chip applications at chip and wafer level. This includes complex 2.5D and 3D IC packages, Focal Plane Arrays (i.e. image sensors), MEMS/MOEMS, and more.
Placing small devices on large substrates is made possible by the FPXvisionTM optical system design. With this alignment system, the smallest structures at the highest magnification can be viewed across the entire field of view. Moreover, FPXvisionTM introduces pattern recognition to a die bonder with manual alignment.
The FINEPLACER® sigma embraces all features of an assembly and development platform capable of handling an unlimited spectrum of applications and prepared for future technologies.
Contact Us
Key Facts*
- Large bonding area
- Reproducible sub-micron placement accuracy
- Pattern recognition for software verified alignment
- Wide range of supported component sizes
- UHD vision alignment system with FPXvisionTM
- Modular machine platform allows in-field retrofitting during entire service life
- Wide range of component presentation (wafer, waffle pack, gel-pak®)
- Synchronized control of all process related parameters
- Process module compatibility across Finetech platforms
- Individual configurations with process modules
- Ultra low bonding force
- Data/media logging and reporting function
- Wide range of controlled bonding forces
- In-situ process observation in HD
- Full process access & easy visual programming with touch screen interface
- Numerous bonding technologies (adhesive, soldering, thermocompression, ultrasonic)
- 3-color LED illumination
- Sequence control with predefined parameters
*depending on configuration
Videos
By using this element, you agree that your data will be transmitted to external services (https://www.youtube-nocookie.com) and that you have read our privacy policy.
Applications & Technologies
With a broad range of supported applications and technologies, our die bonding systems are ready to tackle any application challenge in the industry. And as market requirements shift and new technologies emerge, their modular hardware and software architecture ensures maximum technological versatility over the entire service life.
- Micro-optical bench assembly
- IR detector assembly
- Gas pressure sensor assembly
- VCSEL/photo diode (array) assembly
- Visual image sensor assembly
- Generic MEMS assembly
- Micro optics assembly
- Single photon detector assembly
- Ultrasonic transceiver assembly
- Laser diode assembly
- µLED (array) assembly
- Laser diode bar assembly
- High-power laser module assembly
- Acceleration sensor assembly
- Generic MOEMS assembly
- Ink jet print head assembly
- X-Ray detector assembly
- Optical sub assembly (TOSA/ROSA)
- E-beam module assembly
- Mechanical assembly
Functions - Modules - Enhancements
Our die bonding solutions are as individual as our customers’ requirements and offer a wide range of configuration options. In addition to the system’s basic functions, which are part of the standard functional range, numerous process modules are available for each system, expanding the spectrum of applications. Retrofittable at any time, they enable additional die bonding technologies and processes either directly or as part of a module package. A selection of functional enhancements and accessory systems make daily work with the die bonder easier and help to make certain technology and process sequences even more efficient.
- Automatic Dipping Unit
Motorized dipping unit for viscous materials like flux or adhesives. Suitable for use with stamping tools or for direct dipping of various sized components. Adjustable for dipping baths with different thicknesses.
- Automatic Tool Changer
Use different tools or tool tips, automatic exchange in process.
- Automatic Tool Changer
Use different tools or tool tips, automatic exchange in process.
- Bar Code Reader "SmartIdent"
Enhances the functionality of the operating software. It enables a fast and safe identification of any board based on their unique bar code label(s).
- Bonding Force Module (automatic)
Enhances the existing bond force range and allows the use of software controlled process forces.
- Bonding Force Module (manual)
Provides various bonding force ranges and allows the mechanical adjustment of different process forces.
- Camera Module (3D)
For determining spatial coordinates of objects to be processed using image recognition (RGB lighting).
- Camera Module (Up-Looking)
For determining surface coordinates on the underside of captured objects using image recognition (RGB/coaxial illumination).
- Camera Y-Shift Module
Allows extending the field of view in Y-direction.
- Chip Heating Module
Direct contact heating from the top with chip specific tool design to apply temperature from the chip side. E.g. used for thermocompression, gluing or ACA bonding
- Component Presentation
Allows presentation of components via Gel-Pak®, VR trays, waffle packs or tape holders as well as the support of dipping trays.
- Die Eject Module with Carousel
Used to pick up components with the placement arm directly from blue tape with the use of different eject tools. Supports snap rings and wafer frames.
- Die Eject Module
Used to pick up components with the placement arm directly from blue tape. Supports snap rings and wafer frames.
- Die Flip Module
Allows flipping of components prior to face-down assembly.
- Direct Component Printing Module
Applying solder paste made easy by printing directly on the component | An “all in one“ solution for reworking QFN, SON and MLF components.
- Dispense Module
Integration of dispensing systems for applying adhesive, flux, solder paste or other pasty material. Various supported types like time-pressure, volume and jet dispensers.
- Dual-Camera Optics
Together with the main camera, the additional camera allows two object field sizes without zoom or different object field positions. Improves the display of large objects and thus accelerates the workflow.
- FPXvisionTM
Ensures a high resolution at all magnification levels.
- Flip Chip Test Module
The “Known Good Die" testing allows chip probing / testing prior to the bonding process.
- Form Generator
Software extension for creating and using virtual forms in the camera image to support relative and face-up alignment processes.
- Formic Acid Module
Creates an inert or reactive (CH2O2) process atmosphere. Used to reduce and prevent oxidation during soldering (e.g. eutectic or indium bonding). Add-on for Substrate Heating Modules.
- Gap Adjustment Module
For precisely setting a defined gap between component and substrate.
- HEPA-Filter
Integrated HEPA filter for cleaning the atmosphere in a closed system. Enables clean room conditions and reduces particle contamination.
- Handling Module
Used to handle substrates or components independently from the bonding tool.
- Height Scanner (3D camera)
For determining heights, lengths and coordinates of objects to be processed by image recognition (RGB illumination/coaxial illumination).
- Height Sensor (Autofocus)
Allows automatic focus setting of component and substrate as well as height measurements.
- Height Sensor (Laser)
Allows sensing of heights by means of Laser triangulation for measuring purposes.
- Height Sensor (mechanical)
For determining heights, lengths and coordinates of objects to be processed by mechanical path measurement.
- High Resolution Optics
Allows using different achromatic lenses to adapt the field of view and optical resolution.
- I/O Lift System
Automatic substrate or boat unloading from magazines / loading into magazines.
- I/O Panel Handling System
Automatic loading and unloading of large panels or substrates.
- ID Code Reader
Allows reading of ID codes of various types like barcodes, 2D-codes and RFIDs.
- Indexer/Conveyor
For automatic loading / unloading of substrates. Width-adjustable for various substrate dimensions.
- Laser Activation Module
Activation / ignition of reactive materials such as nanofoils by laser pulse.
- Laser Bottom Heater
Allows ultra-fast heat cycles du to an integrated high power laser source.
- Lift Station
Lifting objects from conveyor units into a processing position.
- Lifting Door
Lifting door with sliding motion to minimize external effects like particles or temperature changes. Can be opened also partly for optimized access and interaction. Reduces the space required in the installation area.
- Manual Dipping Unit
Manual squeegee units for viscous materials like adhesives or flux. Suitable for use with stamping tools or for direct dipping of various sized components. With adaptable layer thicknesses.
- Mask Generator "Scaled"
Software extension for creating and projecting virtual masks to simplify alignment processes. These masks can be combined to scale from several objects.
- Motorized Nick & Roll Motion
Tilting unit with motorized angular adjustment in the axes phi(X) and phi(Y). This nick and roll movement can be used for parallel positioning or for bonding at certain angular positions.
- Motorized Z Table
Positioning table with motorized z-travel for automatic working height adaptation; with manual x, y adjustment via micrometer screws.
- Optics Shifting
Allows to adjust different camera positions along the x-axis of the system. Useful to align large components with maximum magnification.
- Optics Shifting
Allows to adjust different camera positions along the x-axis of the system. Useful to align large components with maximum magnification.
- Overlay vision alignment system (VAS) with fixed beam splitter
Precise visual alignment of chip and substrate.
- Pattern Recognition
Software tool to recognize various alignment marks. Used to control the position or alignment between component and substrate.
- Plasma Cleaning
Preparation of assembly surfaces using atmospheric plasma for better wetting during joining processes.
- Precision Scale
SPC (Statistical Process Control) for dispensing volumes in the automatic process flow.
- Process Gas Module
Controls an inert or reactive (H2N2) atmosphere in an enclosure or with the bond head. Used to prevent or reduce oxidation during soldering or bonding.
- Process Gas Selection
Enhances a process gas module to handle two different gases for programmed selection in the process.
- Process Video Module
Allows the in-situ observation of the working area during the bonding process.
- Process Video Module
Allows the in-situ observation of the working area during the bonding process.
- Programmable Wafer Changer with Cassette Lift
Accommodates 300 mm wafer cassettes. Programmable speed and slots.
- Scrubbing Module
Improve the wetting condition of bonding surfaces and reduces voids. Oxide layers are scrubbed off in a low frequency mechanical sonic process.
- Solder Removal Module
Removed in one sweep | Allows precise residual solder removal in an inert atmosphere*. Molten solder is easily removed from the board with powerful vacuum without disturbing any pads or solder resist.
- Substrate Heating Module
Various direct contact heating options to heat up substrates from the bottom during the process. Substrate-specific fixations available. Optionally with process gas integration. Used e.g. for thermocompression, thermal adhesive or thermosonic bonding.
- Substrate Support
Unheated support plate with substrate specific fixation (e.g. vacuum) to clamp various substrates.
- Target Finder
A small red point accelerates the working flow | Enables coarse position alignment of the table to the tool with the help of a laser spot.
Read more (PDF, 0.3 MB) - Tool Tip Changer
Use different tools or tool tips in process.
- Traceability Module
Automatic tracking and logging of all process relevant parameters (e.g. temperature, force, etc.) as well as associated component details (e.g. serial numbers).
- Tray & Tape Feeder
Infeed/outfeed of objects for automatic processing in larger quantities on a minimal presentation area.
- UV Curing Module
Provides ultra violet LED-light in various wave lengths for adhesive processes without thermal influence. The UV source can be attached to the tool or mounted to the substrate holder.
- Ultrasonic Module
Enables ultrasonic or thermosonic bonding. Transmits mechanical energy based on lateral movement of the ultrasonic transducer to the component while it is in contact with the substrate.
- Vacuum Chamber Module
Enables bonding processes within a system integrated vacuum chamber. No extra handling steps and fully software controlled.
- Wafer Changer
Accommodates 300 mm wafer cassettes. Programmable speed and up to 24 slots.
- Wafer Heating Module
Special substrate heating module designed for large wafers. Very uniform heat distribution during chip to wafer or wafer to wafer bonding.
- Wafer Table
Automatically positions and indexes the wafer over the Die-Ejector.
- Zoom Optics
Allows the adaptation of the Vision Alignment System for an optimized view of components and substrates.
Technical Paper
Focal Plane Array (FPA)
Eutectic Bonding with Au/Sn
Ultrasonic Die Bonding
Copyright © 2025 Finetech GmbH & Co. KG, All rights reserved.